Разновидности котельных
Каждая котельная представляет собой здание, предназначенное для выработки теплоносителя. Помещение может быть расположено в основном объекте или вынесено на отдельную территорию. Работа котельных основывается на использовании специализированного оборудования, где в качестве топлива может быть применен твердый, жидкий или газообразный материал. Наличие таких комплексов позволяет поддерживать тепло в отдельных частных домах, целых населенных пунктах или промышленных объектах. Перемещение теплоносителя осуществляется по трубопроводам, расположенным в теплотрассах.
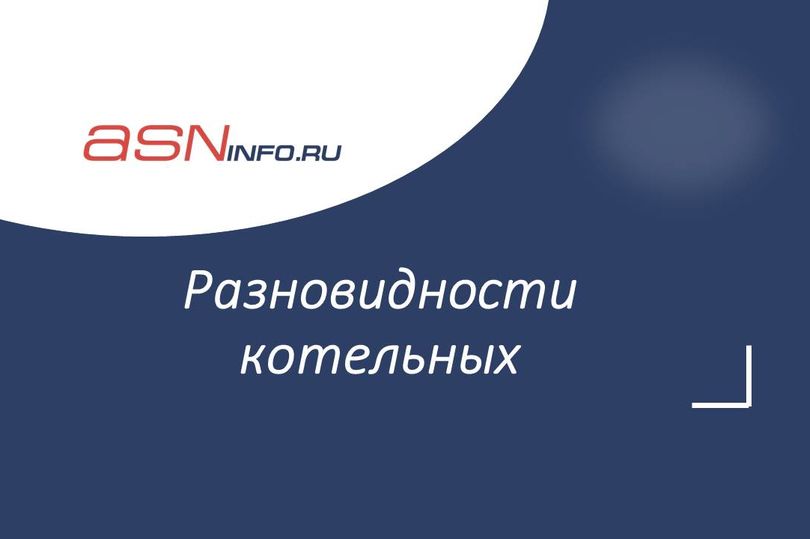
Работа котельных
Каждый населенный пункт или промышленный объект требует отопления. Именно такие функции возлагаются на котельные, которые могут быть разного масштаба. Некоторые из них обслуживают малое количество домов, а другие — большие промышленные предприятия. В качестве теплоносителя может выступать вода или пар, а подогрев осуществляется в установленных котлах, где происходит сжигание различного вида топлива.
Котельная представляет собой сложное инженерное сооружение, которое требует разработки серьезного проекта, соответствующего требуемым нормативам. На основании созданных чертежей, которые предварительно проходят экспертизу в государственных органах, происходит строительство здания и установка запланированного оборудования. Кроме основных агрегатов, к которым относятся котлы, вырабатывающие тепловую энергию, устанавливаются дополнительные приборы. Сюда включаются теплообменники, емкости, насосы, запорная арматура. Доставка нагретой воды осуществляется по трубопроводам. Они прокладываются по теплотрассам и состоят из отдельных участков, соединенных между собой специальными муфтами.
Разновидности котельных
Современные котельные имеют большое количество разновидностей. Различаются они в зависимости от используемого топлива, типа теплоносителя, а также места размещения. При этом основным параметром является расстояние от котельной с установленным оборудованием до отапливаемой территории. Оно должно соответствовать разработанным нормам, поэтому проектировщики всегда ориентируются на существующую документацию. В том случае, когда отапливаемый объект имеет небольшие размеры, котельная занимает часть территории здания. Только при обслуживании крупных промышленных предприятий или больших населенных пунктов строится отдельное сооружение.
Газовые
Использование в качестве топлива газа позволяет существенно увеличить мощность котельных. Кроме того, обеспечивается экономия и отсутствует загрязнение окружающей среды. Принцип работы газового оборудования заключается в следующем:
- На горелку котла из трубы поступает газ, который сгорает в камере и этим нагревает теплоноситель, циркулирующий по теплообменнику оборудования.
- Разогретый до нужной температуры теплоноситель движется в направлении коллектора, от которого отводится ряд отопительных контуров.
- Проходя через ответвления, теплоноситель постепенно охлаждается, нагревая отопительные контуры.
- На последнем этапе охлажденный теплоноситель возвращается в котел с целью последующего нагрева.
На этом этап работы заканчивается и тут же начинается новый цикл. В состав газовых котельных входят следующие виды оборудования:
- Регуляторные установки. Это агрегаты, обеспечивающие в системе постоянное давление газа.
- Газорегуляторные пункты. Оборудование, отвечающее за очистку поступающего газа. При необходимости оно может остановить протекающий процесс в автоматическом порядке.
- Фильтры. Устанавливаются перед запорной арматурой с целью задержания посторонних предметов.
Газ, как топливо, обладает повышенной горючестью, поэтому ко всем котельным установкам предъявляются очень высокие требования.
Жидкотопливные
В качестве жидкого топлива чаще всего используется дизельное горючее. Это очень доступный вариант, поскольку солярку всегда можно купить и удобно хранить. Чаще всего дизельное топливо используется при оборудовании домашних котельных или в случае отопления промышленных объектов.
Также в качестве горючего может быть использовано отработанное масло, которое хорошо работает в котлах. Применяется оно в тех случаях, когда использование по назначению уже становится невозможным. Очень редко в качестве жидкого топлива используются мазут и нефть. Исключение составляют только тепловые электростанции.
Во время монтажа жидкотопливных котельных обязательно следует продумывать хранение горючего. Для его содержания специально устанавливаются недалеко от объекта баки, сделанные из металла, пластика или стекловолокна. Монтаж возможен на земле или в небольшом углублении.
При попадании топлива в камеру котла оно сжигается, что приводит к формированию тепловой энергии. При этом горючая смесь поступает вместе с воздухом, который предварительно проходит очистку. На следующем этапе происходит нагрев теплоносителя, который начинает свою цикличную циркуляцию.
Твердотопливные
Если котельная работает на твердом топливе, то для сжигания используются древесные щепы, уголь или специальные гранулы. Во время их сгорания энергия преобразуется в тепло, подогревающее воду или пар. Работа такого оборудования имеет КПД, составляющее порядка 90%, что немного ниже, чем при использовании солярки или газа. При этом цена на твердое топливо полностью компенсирует такой недостаток. Установленная система имеет несложную конфигурацию, в которой отсутствуют многие дорогостоящие компоненты. Здесь нет баков-накопителей и топливных насосов.
Мощность котельной, работающей на твердом топливе, обычно составляет интервал 100 кВт-20 МВт. Подача горючего происходит в ручном или полуавтоматическом режиме. В зависимости от размера загрузочной камеры, повышается или понижается выработка котлом тепла в единицу времени.
В качестве оборудования используются котлы КВМ. Поступающее топливо здесь равномерно распределяется по колосниковому полотну. Образующийся шлак и зола через некоторое время удаляются вручную, путем поворота колосника, установленного на оси. Обычно такого типа котельные создаются в организациях с небольшим бюджетом, которые не могут себе позволить приобретать дорогостоящее оборудование.
Паровые
В специальных установках происходит формирование из воды пара, который поступает в циркуляционную систему. Работают такое оборудование на разных видах топлива. В котлах может формироваться два вида пара:
- Насыщенный. Чаще всего используется в бытовых и коммунальных службах.
- Перегретый. Применяется на объектах промышленного масштаба.
При этом в оборудовании может присутствовать давление следующей силы:
- Низкое. Составляет порядка 1 атм.
- Высокое. Находится в интервале от 1 до 10 атм.
- Сверхвысокое. Оно равняется 18-20 атм.
Котел выглядит в виде сосуда, где происходит процесс превращения воды в пар. Внутри проложена система труб, имеющая широкий диапазон размеров. В состав котельной установки кроме основного оборудования входят дополнительные агрегаты:
- Пароперегреватель. Устройство нагревает воду свыше 100°. В результате формируется пар, температура которого составляет 500°. Иногда такие агрегаты встраиваются в общую установку или могут располагаться отдельно.
- Паровой сепаратор. Здесь из пара удаляется вся оставшаяся жидкость с целью максимального обезвоживания. В результате эффективность котла существенно повышается.
- Аккумулятор. Его наличие стабилизирует работу оборудования. Сначала им поглощается выработанный избыточный пар и по мере необходимости обратно возвращается в систему.
- Водоочиститель. Присутствие такого прибора уменьшает наличие в воде различных примесей, что снижает со временем в котле количество накипи.
Кроме того, в состав оборудования входят клапаны, воздухонагреватели, блоки управления системой и регуляторы использования энергоресурсов.
Водогрейные
В водогрейной котельной используется оборудование специальной конструкции. Здесь устанавливаются котлы, в которых ведется подогрев жидкости до температуры 95°. Временами этот показатель увеличивается и превышает 115°, но за счет высокого давления закипания жидкости не происходит, и это исключает ее превращение в пар.
Водогрейные котельные разделяются на два типа:
- Водотрубные. Теплоноситель движется трубкам, которые располагаются внутри котла, а нагревается он в результате сгорания топливной смеси.
- Жаротрубные. В этом случае по установленным трубкам передвигаются уже продукты сгорания горючего, а теплоноситель располагается снаружи и нагревается от соприкосновения с металлом.
В качестве исходного топлива может быть использован газ, уголь, топливные гранулы, мазут и солярка.
Водогрейные котлы имеют высокий коэффициент полезного действия. Этот показатель достигается в результате небольшого количества теплопотерь. Такие виды котельных разрабатываются 3 типов:
- Для отопления населенных пунктов. Размер котельных зависит от площади отапливаемой территории.
- Для отопления крупных промышленных комплексов. Это крупные системы, способные обеспечить обогрев масштабных производственных предприятий.
- На теплоэлектростанциях. Такие системы вырабатывают горячий пар, необходимый для функционирования электрогенераторов.
Коэффициент полезного действия водогрейных котельных может достигать 93%.
Комбинированные
Котельные такого типа способны вырабатывать разные виды теплоносителей, к которым относятся вода или пар. При этом работают они на двух видах топлива. Один тип у них считается основным, а второй — резервным. Именно поэтому такие котельные получили название комбинированные. Чаще всего для работы используется дизельное горючее и газ.
Комбинированные котельные чаще всего используются для отопления ответственных промышленных объектов. Связано это с тем, что в случае перебоев с поставками основного горючего всегда можно перейти на резервный вариант. В результате у производственного предприятия исключаются возможные экономические потери.
Обычно в качестве основного топлива используется газ потому, что он является наиболее экологически чистым горючим. Дизельное топливо удобно применять как запасной вариант ввиду его доступности. Использование твердого топлива на комбинированных котельных наблюдается редко. Иногда такое происходит на начальном этапе с перспективой дальнейшего перехода на газ.
На диатермическом масле
Иногда в качестве теплоносителя используется диатермическое масло, обладающее особыми физическими характеристиками. Преимущества такого материала заключаются в следующем:
- Высокая плотность. Этот параметр значительно превышает показатель воды.
- Длительное время удерживает тепло и очень медленно охлаждается.
- Теплоноситель способен разогреваться до температуры 300-360°.
- На поверхности металла от диатермического масла не остается накипи.
При использовании термомасла следует постоянно следить за его качеством и регулярно проводить замену. Кроме того, требуется постоянно наблюдать за состоянием трубопровода из-за повышенного его нагрева. С этой целью сюда ставятся бесшовные трубы, изготовленные из стали Ст. 20. Данный материал является пороговым, который подвергается цементации на глубину 1-1,5 мм.
Повышенные требования предъявляются к запорной арматуре, разработанной с учетом ее возможности выдерживать большие температуры. Во всех установленных клапанах присутствуют пневматические приводы регулирования. Проектирование котельных такого типа совершается не только по классическим нормам, но и с учетом особенностей характеристик теплоносителя.
Особенности блочно-модульных котельных
Блочно-модульные котельные относятся к зданиям облегченной категории. Фактически это передвижные помещения, полностью готовые для работы. Изготавливаются они из легких панелей, скрепленных между собой уголками разного размера. Конструкции обладают универсальностью и легкостью.
Такие системы не имеют больших затрат на обслуживание. Они часто оснащены блоком управления, который выполняет следующие функции:
- осуществляет непрерывный контроль над работой приборов;
- ведет управление всеми котлами;
- проводит подключение в случае необходимости резервных контуров;
- отключает подачу газа при возникновении аварийной ситуации.
Блочно-модульные котельные представляют собой конструкции, состоящие из отдельных составляющих. После изготовления они могут по отдельности транспортироваться в предназначенное место различными видами транспорта, что представляет большое удобство. Затем они составляются, образуя единое целое.
Встроенные котельные
Если в здании имеется свободное пространство, то сюда можно устанавливать встроенные котельные. Обычно это делается в тех случаях, когда отсутствует возможность подключения к централизованному отоплению. Для такой цели подойдет территория любого этажа, где есть возможность установить оборудование. При расчете обязательно следует в качестве исходных данных закладывать нужную мощность котельной, чтобы она обеспечивала подачу тепла на все помещение.
Однако для встроенных котельных существует ряд ограничений. Их не допускается устанавливать на следующих территориях:
- В школьных заведениях, учебных учреждения и многоквартирных домах.
- В оздоровительных организациях.
- В различных общественных и административных зданиях. Также нельзя устанавливать такие котельные на смежных с ними территориях. Однако это невозможно только в том случае, когда на них проживает более 50 человек.
Во время установки оборудования следует придерживаться следующих условий:
- Водонагревательные котлы должны иметь ограничение по нагреву 115°.
- Паровые установки — создавать давление не выше 70 КПа.
- Предел мощности для котлов, работающих на жидком или газообразном топливе, должен быть не больше 3 МВт.
- Если оборудование работает на твердом топливе, то предел его мощности должен составляет 1,5 МВт.
Данные положения для встроенных котельных являются обязательными.
Крышные конструкции
Более подробно о них мы рассказывали здесь. Обычно крышные котельные оборудуются в специально отведенном месте помещения. Это может быть не только крыша, а и подвал. Их задача состоит в выработке необходимого количества тепла, чтобы они полностью обслужили территорию. Это может быть промышленное предприятие или большой жилой район.
Для обустройства крышных котельных выдерживайте следующие требования:
- полное соблюдение всех норм пожарной безопасности;
- вывод газовых отходов исключительно через крышу;
- дверные приемы оборудованы так, чтобы через них свободно могло пройти любого размера оборудование;
- в каждом из агрегатов наличие всех датчиков и регуляторов, которые предусмотрены на основании технологической схемы.
Для такого вида котельных устанавливается оборудование повышенной мощности, которое может вырабатывать большое количество нагретой воды и пара. Примером являются котлы Clever L, о которых хорошо рассказано здесь.
Итого, каждая котельная представляет собой помещение, состоящее из целого технического комплекса. Основной фигурой в нем является котел. Также здесь присутствует дополнительное оборудование и трубопроводы. Чтобы вся система работала надежно, требуется поддерживать ее в надлежащем техническом состоянии.
Асфальтирование
Чтобы дорожное полотно прослужило длительное время, оно сверху покрывается асфальтом, представляющим собой застывший специальный раствор. Данный процесс носит название асфальтирование. Как только покрытие затвердевает, образуется ровное твердое пластичное полотно, на котором длительное время не появляются трещины. Чтобы его качество соответствовало стандартам, все работы выполняются в точности с разработанной технологией. Каким образом проводится дорожное строительство, хорошо описано здесь.
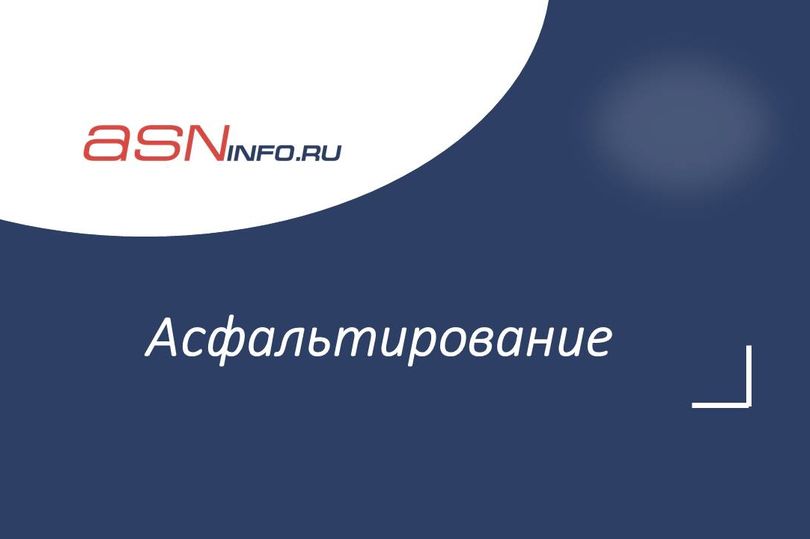
Характеристика смеси
Существуют разные технологии изготовления раствора для укладки асфальта. При этом всегда основными компонентами являются битум, песок, щебень и добавки. Наиболее качественной технологией является изготовление литого асфальтобетона. В него входят те же составляющие, но к их качеству предъявляются повышенные требования.
Уложенный на поверхность раствор с течением времени затвердевает. В результате формируется цельное покрытие. Основное преимущество литого асфальтобетона — герметичность, поскольку затвердевшая поверхность не пропускает влагу. Это является очень важным моментом. Проникающая через микротрещины вода зимой превращается в лед. Многоразовое замораживание и оттаивание плохо сказываются на дорожном полотне.
Толщина укладываемого асфальта должна составлять от 80 мм. Если такое условие не будет выдержано, то от ударной нагрузки проезжающих автомобилей оно быстро придет в негодность. При полном соблюдении технологии время эксплуатации асфальтобетона может достигать 9 лет. За этот период величина износа полотна может достигать 6 мм, что не выходит за пределы допуска. Если асфальтирование ведется в ответственных местах, то иногда следует укладывать два слоя раствора. Постепенно они спекаются между собой, формируя цельное соединение.
Составляющие раствора
Основным связующим звеном всех составляющих асфальтобетонной смеси является битум. Без этого компонента застывший раствор не будет обладать характеристиками, присущими асфальту. Получится обычный бетон, не обладающий пластичностью. Кроме битума асфальтобетонный раствор состоит еще из следующих веществ:
- песка;
- щебня;
- добавок.
Процентное содержание всех компонентов в каждом конкретном случае может меняться. Это зависит от степени нагрузки на асфальтируемую территорию.
Битум
Связка всех компонентов раствора обеспечивается присутствием битума. Это вязкий материал, который еще носит название мазут. Получается он искусственным путем методом перегонки нефти. В процессе проведения крекинга мазут является конечным продуктом. Получаемый битум бывает множества разновидностей. Каждый материал имеет свой класс и маркировку. Все эти параметры отражаются в ГОСТ 22245-90. С учетом уровня асфальтируемой дороги подбирается соответствующего качества и битум. В первую очередь здесь учитываются климатические условия региона, поскольку в сильные морозы нагрузка на покрытие резко возрастает.
Задача битума состоит в обволакивании твердых частиц раствора с последующим их удержанием в связке. От этого во многом зависит стойкость и пластичность будущего асфальта.
Если процедура укладки раствора проводится в морозную погоду, то в битум добавляется растворитель, который носит название эмульгатор. В результате у раствора появляется морозоустойчивость. Особенностью эмульгатора является его способность растворяться в воде с последующим испарением. В конечном итоге он удаляется из застывшего асфальта, но нужные характеристики у покрытия сохраняются.
Песок и щебень
При создании асфальта подбору песка уделяется серьезное внимание. Особенно это касается тех случаев, когда ведется укладка литого асфальта. Чтобы обеспечить песку нужные характеристики, он изготавливается искусственно. Происходит это путем измельчения твердых камней горных пород. Также исходным сырьем может служить отсев.
Допустимо применение песка естественного происхождения, но при условии, что он будет отвечать всем необходимым характеристикам. В первую очередь обращается внимание на его чистоту и полное отсутствие в нем грязи. Также все элементы фракции должны быть одинакового размера. Эти условия зафиксированы в нормативных документах, на которых ведется ориентирование при проверке качества песка.
Щебень относится к более крупной составляющей. Изготавливается он из морозостойких горных пород, прочность которых составляет 120 МПа. При выполнении этих условий уложенный асфальтобетон способен выдерживать около 50 циклов заморозок и оттаиваний.
Также щебень может изготавливаться из доменного шлака прочностью 80-100 МПа. Во время проверки щебня уделяется внимание конфигурации его зерен. Каждое из них должно иметь форму тетраэдра с острыми кромками или куба. Количество плоских составляющих может быть не более 15% от общей массы. При отсутствии щебня его часто заменяют гравием. Однако перед применением с ним проводится дробление. Делается это с целью формирования у зерен острых кромок.
Добавки
Обязательным условием высокого качества асфальтобетона является наличие добавок. Это могут быть различные целлюлозные волокна, повышающие пластичные свойства покрытия.
При изготовлении литого асфальта в качестве добавочной составляющей используется минеральный порошок, задача которого состоит в связке между собой щебня и песка. Кроме того, он взаимодействует с битумом, повышая у конечного продукта гидрофильность. Это достигается путем набухания мельчайших частиц порошка во время контакта с битумом.
Изготавливается минеральный порошок из доломитов или известковых шлаков. Также допускается применять доменные отходы или заменители другого типа, к которым относится топливная зола.
После укладки литого асфальта его поверхность подвергается чернению. Для этого используется щебень, который изготавливается в специальном оборудовании, где он перемешивается с вяжущим веществом. Необходимость чернения полотна состоит том, чтобы усилить контакт асфальтобетона с покрышками автомобилей.
Процесс производства раствора
Изготовление раствора для последующего асфальтирования проводится в следующем порядке:
- Песок смешивается со щебнем, и вместе они перемещаются с помощью транспортера в сушильный барабан для удаления влаги. После окончания сушки смесь в барабане подогревается до требуемой температуры.
- Доведенные до нужного состояния фракции поступают в смесительный барабан. Параллельно такая же процедура проводится с добавками, из которых также удаляется влага. Затем они транспортируются в смесительный барабан, где соединяются с песком и щебнем.
- Готовый раствор помещается в транспортное средство, которое доставляет их к месту укладки.
Если расстояние от точки изготовления асфальтобетона до рабочей территории небольшое, то в качестве транспортного средства могут использоваться самосвалы. Когда проводится укладка литого асфальтобетона, то для этой цели чаще используются кохеры. На таком оборудовании установлена специальная бочка, в которой смесь постоянно перемешивается и подогревается до требуемой температуры. В результате готовый раствор не теряет своих характеристик по мере транспортировки. Это очень важно для формирования качественного конечного покрытия.
Разновидности смесей
Производимые асфальтобетонные смеси разделяются на 5 типов:
- I тип. Изготавливаемый раствор используется для укладки на автомобильных трассах или мостах. Размеры щебня в такой смеси составляют 5-15 мм.
- II тип. Гранулы щебня здесь доходят до 20 мм. Доставка к месту работы ведется автотранспортом, покрытым защитным тентом. Такой раствор после укладки нуждается в виброуплотнении.
- III тип. Это особый вид раствора, который используется для асфальтирования аэродромов. Размер гранул щебня составляет порядка 40 мм.
- IV тип. Здесь фракция щебня не превышает размеры 5 мм, поэтому такое покрытие применяется в неответственных местах. Таким типом смеси покрываются пешеходные дорожки или полы в квартире.
- V тип. Максимальная величина гранул щебня составляет 20 мм. Основное применение такого типа раствора — для покрытия асфальтобетоном пространства между рельсами трамвайных путей.
Каждый тип смесей используется для укладки на конкретных участках территории.
Используемое оборудование
Для качественного нанесения покрытия применяется специализированное оборудование. В первую очередь это касается укладки литого асфальтобетона. Для работы используют следующие агрегаты:
- Кохеры. Такая техника в основном требуется для перевозки литого асфальтобетона, чтобы он не потерял в процессе транспортировки своих параметров. Для этого сверху устанавливается бочка объемом от 500 до 12000 л. В процессе движения она вращается. Это обеспечивает постоянное перемешивание раствора, чтобы он в дороге не схватился. Кроме того, смесь подогревается для поддержания нужной температуры.
- Гудронаторы. Это тоже автомобили с бочками, из которых удобно вести разлив смеси для укладки на дорогу.
- Асфальтоукладчики. У данного оборудования присутствует жаростойкая резина, выдерживающая высокую температуру. Скорость движения алфальтоукладчика во время работы составляет 3 м/мин.
- Рециклеры. На машине установлена вращающаяся бочка, а смесь в ней перемешивается с помощью имеющихся лопаток. Здесь также предусмотрен ее подогрев.
- Автомобили-ремонтеры. Данные транспортные средства относятся к универсальному оборудованию, поскольку с их помощью ведется не только доставка смеси к месту работы, а и укладка.
Иногда для работы привлекаются финишеры. Обычно в них необходимость возникает при укладке асфальтобетона на железнодорожных мостах. Более подробно об особенностях работы спецтехники при формировании дорожного покрытия мы писали здесь.
Этапы асфальтирования
Где бы ни планировалась ведение асфальтирования, такая работа требует составления проекта. В нем утверждается подготовка всех необходимых материалов и планируемые работы. В случае необходимости проводятся геологические исследования местности с целью изучения рельефа и климатических условий. В подготовленных чертежах указывается конструкция будущего дорожного пирога. Асфальтирование относится к сложному процессу, который совершается в несколько этапов.
Подготовка основания
После составления плана непосредственно на месте начинается разработка территории. При необходимости ведется снос строений и вырубка растительности. Иногда процедура включает в себя выемку слоя почвы. Для этой цели часто используется специальное фрезерное оборудование. С его помощью проводится выравнивание участков для устранения существующих перепадов.
Затем подготовленное основание грунтуется. Для этого оно обрабатывается битумной эмульсией. В некоторых случаях укладка асфальтобетона ведется на старое покрытие. Если оно сохранилось в хорошем состоянии, то его можно использовать в качестве базы. Чаще всего так поступают тогда, когда старый слой представляет собой литой асфальтобетон. Такое покрытие обладает долговечностью, поэтому наличие в нем небольших трещин не является критичным. Они просто ремонтируются путем их расширения и последующей заливки раствором.
Чтобы не выйти за пределы размеченной территории, по краям дороги может устанавливаться деревянная опалубка. Ее высота должна соответствовать уровню будущего покрытия. Однако потребность в ней отпадает при использовании колесно-рельсового укладчика.
Процедура укладки
После доставки горячей смеси она высыпается на место укладки вне зависимости от вида транспортного средства. Это может быть самосвал или кохер. В последнем случае снизу открывается люк, и под давлением вращающихся шнеков раствор вытекает из бочки. Основным условием является полная выработка всего горячего асфальтобетона на протяжении одной смены, поскольку смесь не может оставаться в кохере. Если такое допустить, то извлечь ее на следующий день будет невозможно.
После окончания рабочего дня устанавливается деревянный брус. На следующий день он убирается, и застывшее покрытие размягчается для хорошей стыковки с новой порцией разогретого асфальтобетона.
Когда работа ведется с обычным асфальтом, то разравнивание покрытия происходит с помощью дорожных катков. В этом отношении литой асфальт имеет серьезное преимущество, поскольку жидкая масса обладает текучестью, что исключает потребность применения катков. Сразу после застывания формируется необходимая плотность асфальтобетона. При этом в некоторых случаях допускается трамбовка раствора с помощью автоукладчика. Данный процесс происходит с применением вибротрамбовочного бруса, встроенным в оборудовании.
Поверхностная обработка
Чтобы затвердевшему покрытию обеспечить максимальную долговечность, оно дополнительно улучшается. Для обычного асфальта сверху укладывается дополнительный тонкий слой полотна не более 4 см толщиной. Такое покрытие бывает 3 видов:
- В виде жидкой битумоминеральной смеси. В ее состав кроме мазута входят песок и минеральный порошок. Такой раствор хорошо закупоривает все мелкие трещины и поры, защищая поверхность асфальта от проникновения внутрь влаги.
- В состав битумоминеральной смеси добавляйся щебень. Это обеспечивает покрытию лучшее сцепление с покрышками автомобиля.
- Укладывается слой износа. Это мелкозернистая асфальтобетонная смесь, имеющая высокие показатели прочности. Она составляет толщину до 2 см. После прохождения некоторого времени слой демонтируется, и на его место укладывается новый. При этом основное покрытие остается в целостности.
После укладки литого бетона его поверхность подвергается чернению, поскольку такое покрытие обеспечивает плохой контакт с шинами автомобиля. Для этого на поверхность укладывается черный щебень, который специально доставляется самосвалами на объект в горячем состоянии. Затем он втапливается в асфальтобетон, что обеспечивает покрытию повышенную шероховатость.
Последующий ремонт
С течением времени в асфальтированной дороге могут появляться выбоины. Чтобы не совершать демонтаж всего полотна, проводится ямочный ремонт. Такие дефекты следует как можно быстрее устранять потому, что изношенный участок будет постепенно разрастаться. С этой целью яма с помощью отбойного молотка расширяется.
Затем на обработанную поверхность подается под большим напором воздушная струя, чтобы устранить всю имеющуюся грязь. Для этой цели используется компрессор. Все боковые поверхности ямы обрабатываются битумной эмульсией. После этого в подготовленное отверстие заливается горячий раствор.
Во время проведения ямочного ремонта допускается присутствие небольшого количества влаги, поскольку раствор хорошо сцепляется с основанием дороги. Однако нельзя допускать присутствия объемных луж. Связано это с тем, что после их высыхания будут формироваться пузырьки пара, что негативно скажется на внутренней структуре асфальтобетона.
Итого, процесс асфальтирования позволяет любому участку территории приобрести необходимую гладкость, прочность и эластичность. Это создает удобство для перемещения автомобилей. В процессе укладки покрытия необходимо строго придерживаться разработанной технологии. Только в этом случае полотно может послужить длительное время.
